Brass North America have successfully installed and commissioned over 400 Kawasaki, Fanuc, ABB, and KUKA robotic systems.
As experts in robotics, we provide many services, such as end-to-end project management, robotic simulation, robotic reach studies, programming systems with integrated robotic systems for material handling, packing/palletizing, machine tending, material removal, welding arc & spot, dispense, and painting.
By employing 12 highly skilled robot craftsmen US/Canada, Brass North America has been able to provide support to a wide range of manufacturing industries.
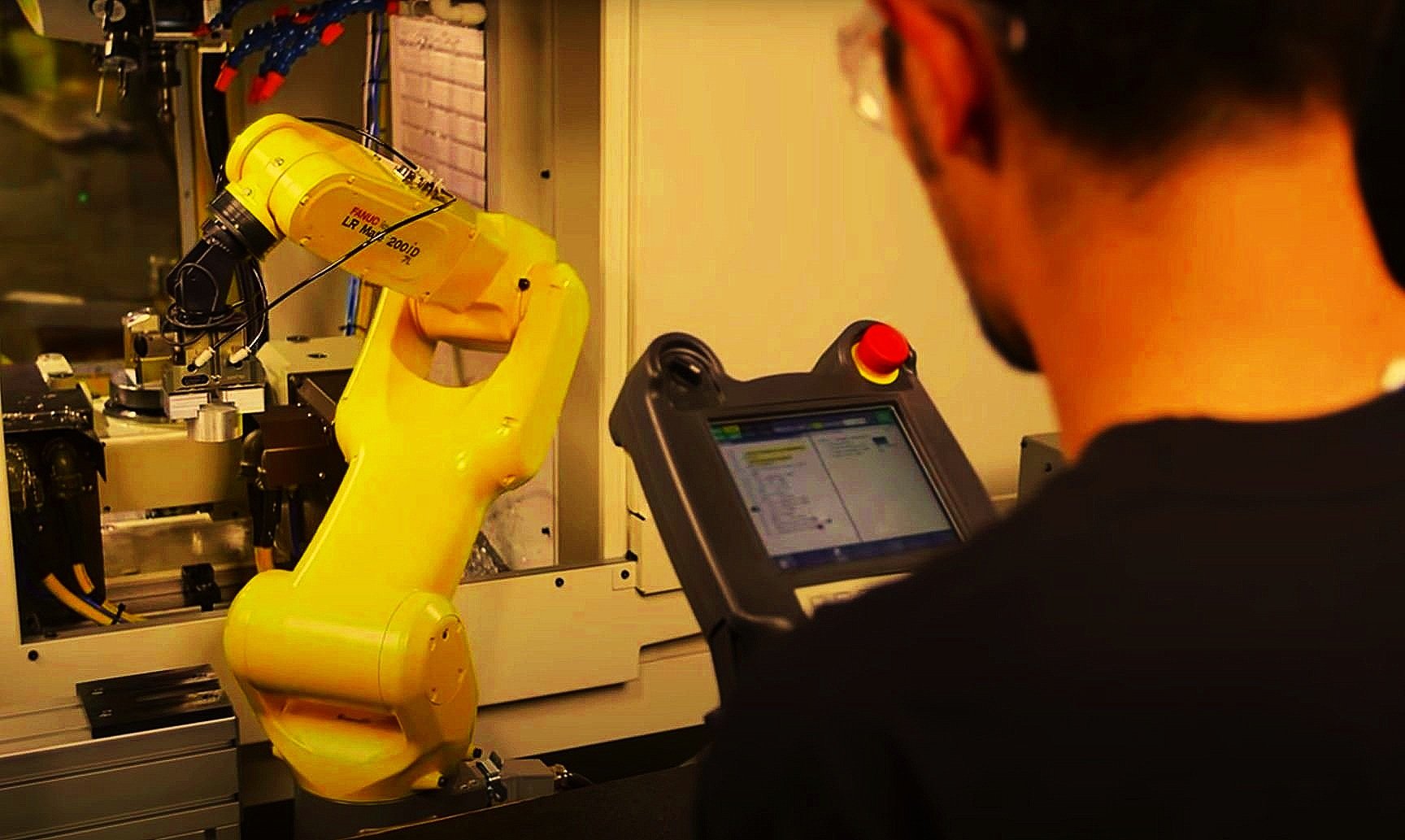
Our services include Robot Offline Programming, Integration, Cycle Time, Production Support, Automation, and many others.
We provide a wide range of robotic services in these robots
-
Fanuc Robotics
FANUC V-500iA, FANUC iRVision 2D/3D, FANUC, CRX Colloborative Robot, DR-3iB, LR, M series
-
ABB Robotics
IRB Series Robots Payload 4kg to 800KG Programming & Integration
-
NACHI
Nachi MZ, NV, MC, CZ, MR, SRA, 600kg with Max reach 2890mm
-
KAWASAKI Robotics
RS & BX Series with S-Controller, F & E controllers programming & integration
-
Robotic Vision System
Fanuc IR vision Robot, Keyence Vision & Cognex vision
-
Robotic Simulation
RoboGuide suite, Siemens ROBCAD, Delmia Robot teaching, validation, offline simulation, Project management, cycle time study & assessment
We offer turnkey automation solutions based on Industrial Robots. Taking advantage of our experience with major industrial automation companies such as Fanuc, ABB, Yaskawa, Kuka, we offer a range of programming solutions as well as simulation & analysis for a wide range of complex applications. Our services are. Additionally, we offer project consultation services to help you implement automation facilities in your production line to improve safety, quality, cost, and delivery.
Robot Simulation and Off-line Programming
We provide simulation and off-line programming services for robotic systems that enable,
3D simulation
Off-line programming
Reachability studies and interference checks
Cycle time optimization
Work cell and workflow layout optimization
Variation simulation analysis
We use Software’s like Delmia, ABB Robot Studio, FANUC Roboguide, KUKA. Sim, Yasakawa Moto SIM EG, Siemens Rob CAD/Process Simulate, RoboDK etc.
Robot On-site Programming
With strong team of Engineers, we provide onsite programming services for robots. On-site robot programming services are mandatory to fine tune the process efficiency. We have skilled Engineers with sound application knowledge to serve you. We provide robot program services for the robots made by ABB, Fanuc, KUKA, Yaskawa, Mitsubishi, others. We also have International Robot Programming experience with multiple companies from Europe. The following applications belong to our areas of expertise:
Assembly Automation
Welding: Mig, Tig Welding & Spot Welding
Cutting: Laser & Plasma
Material handling – Pick & Place, Palletizing
Machine tending – for Press, Injection Molding, Die casting, CNC Machines.
Vision based applications.
Deburring
Dispensing
Inspection
Robot tool design & validation
We design End of Arm Tool (EOAT) based on customer applications and site requirements. The End of Arm Tool is designed based on mechanisms such as vacuum, electromagnetic, servo and mechanical grippers, Weld guns, etc. We offer simulation services for your existing applications to rapidly test algorithms, design robot configuration and perform regression testing using realistic scenarios that enable robust physics engine, high-quality graphics, and convenient programmatic and graphical interfaces.
The Brass North America Robotics Training Program is designed for manufacturing engineers, maintenance workers, and production assistants who operate robots
Industrial robots are becoming increasingly prevalent in manufacturing and other industrial settings. They are designed to perform tasks that are repetitive, dangerous, or too precise for humans to perform. This training content will provide an overview of the different types of industrial robots, their applications, and how to safely operate and maintain them.
Module 1: Types of Industrial Robots
Cartesian robots: These robots have three linear axes that move in a straight line. They are often used for pick-and-place tasks and assembly operations.
Cylindrical robots: These robots have two rotary axes and one linear axis. They are commonly used for welding and painting tasks.
Spherical robots: These robots have three rotary axes and are often used for handling and palletizing tasks.
SCARA robots: These robots have two parallel rotary joints that provide high-speed, accurate movement in a confined space. They are often used for assembly and packaging tasks.
Module 2: Applications of Industrial Robots
Welding: Robots are used to perform precise welding operations on large and small parts.
Painting: Robots are used to apply paint to large surfaces with speed and accuracy.
Assembly: Robots are used to perform repetitive tasks such as screwdriving and fastening.
Palletizing: Robots are used to stack and organize products on pallets.
Packaging: Robots are used to sort and package products at high speeds.
Module 3: Safety and Maintenance
Safety: It is important to follow safety guidelines when working with industrial robots to avoid accidents and injuries. This includes properly securing the robot, keeping the work area clear, and staying out of the robot's work envelope.
Maintenance: Regular maintenance is essential to ensure the robot is operating correctly and to prolong its lifespan. This includes cleaning, lubrication, and checking for wear and tear on the robot's components.
Module 4: Programming and Control
Programming: Robots are programmed using a variety of programming languages, including C++ and Java. Programs are used to control the robot's movements and its interactions with other equipment.
Control: Robots can be controlled using a variety of methods, including teach pendants, hand-held controllers, and computer programs.
Conclusion:
This training content provided an overview of the different types of industrial robots, their applications, and how to safely operate and maintain them. It is important to follow safety guidelines and perform regular maintenance to ensure the robot is operating correctly and to prolong its lifespan. Additionally, understanding the programming and control aspect of industrial robots is important for optimal performance of these machines.